October 20, 2023
Field Trip to Baker's Leather Tannery
Last week was an incredibly exciting week for us here at TBHQ.
We were lucky enough to visit our local Devon tannery and show one of our clients the magic of the tannery whilst they were visiting from Tokyo. A massive thank you to Andrew at J&FJ Baker & Co for taking so much time to show us around and explain the entire process from raw hide to the finest world renowned and highly sought after oak bark tanned leather. What an incredible privilege.
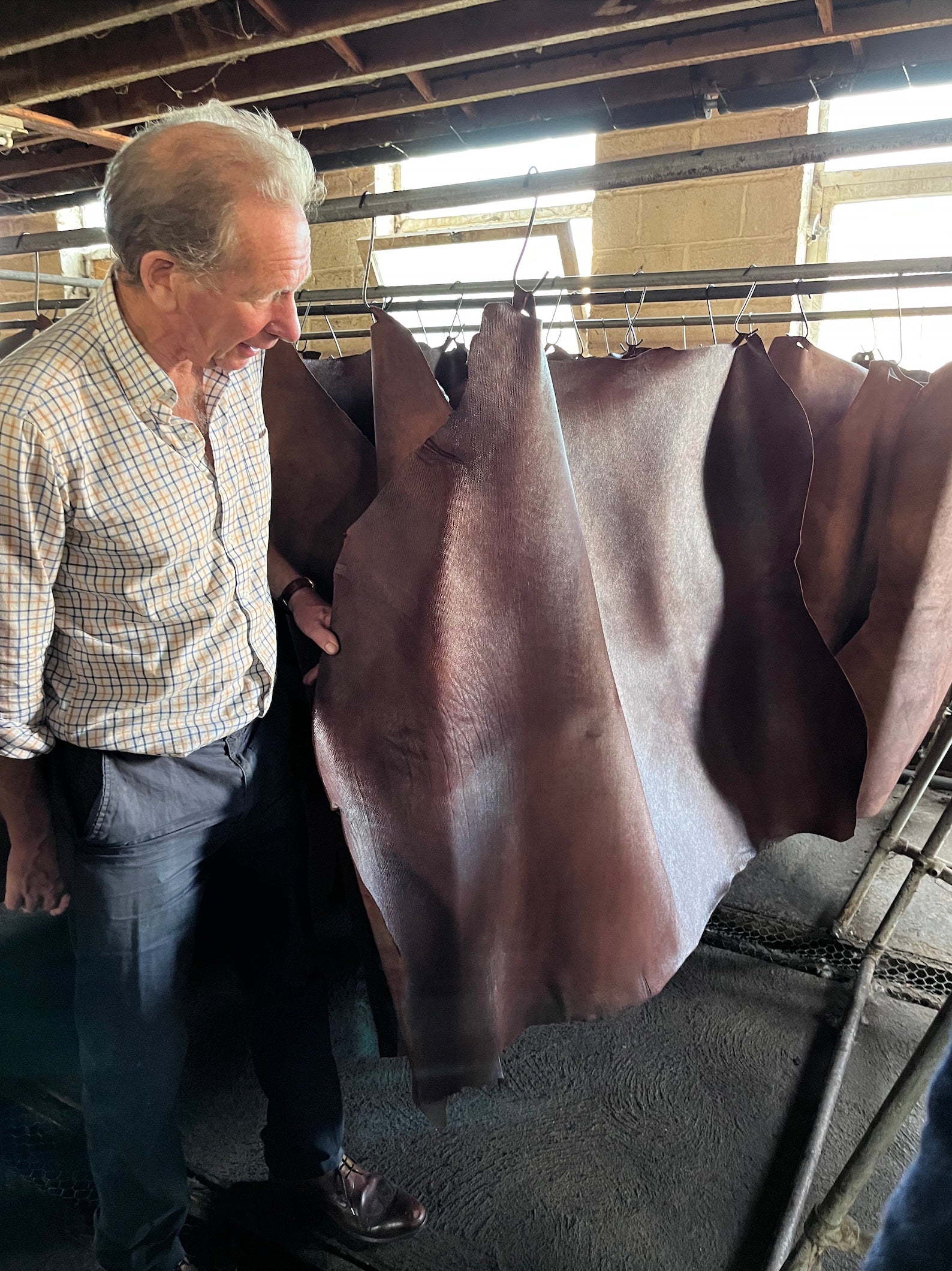
There has been a tannery at the site in Colyton since Roman times, and today the tannery is still family run, 6th generation. Baker's is now the only remaining oak bark tannery in Europe.
The buildings are ancient, as a point of reference, the 'New' Tan Yard is over 120 years old, a lot of the machinery used is also ancient, as are the time honoured techniques of oak bark tanning. This could not be further removed from the automated industrial processes used by modern tanneries to mass produce much of the world's leather.
Sustainable tanning, the old fashioned and chemical free way, with oak bark takes time - over a year to transform each raw hide into the finished article. It is a truly labour intensive, traditional and small scale operation. The leather is hand crafted in small batches, by highly skilled and experienced artisanal tanners. Due to the gentle tannage and full grain nature of this leather preserving all of the natural characteristics, no two hides are the same.
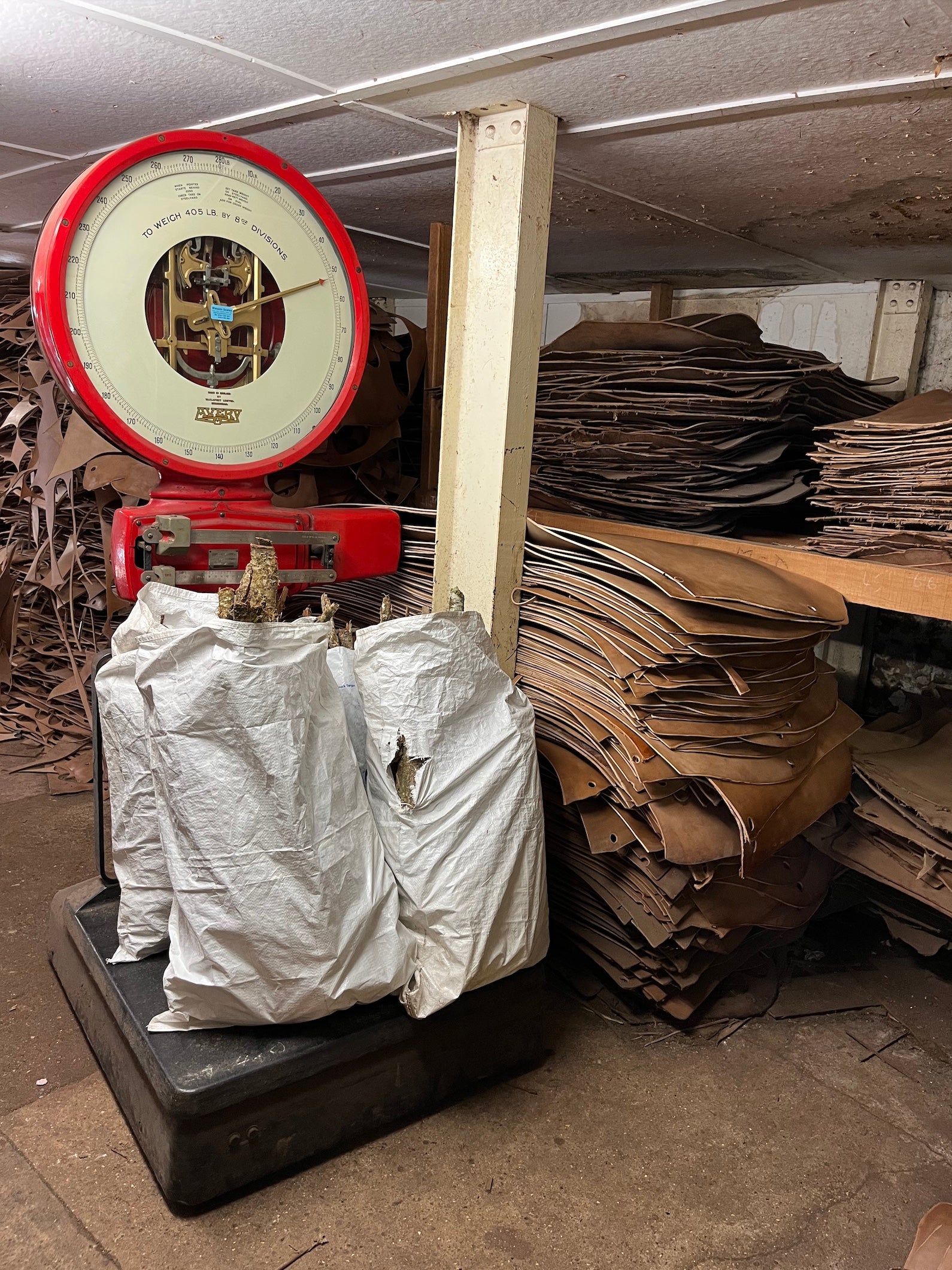
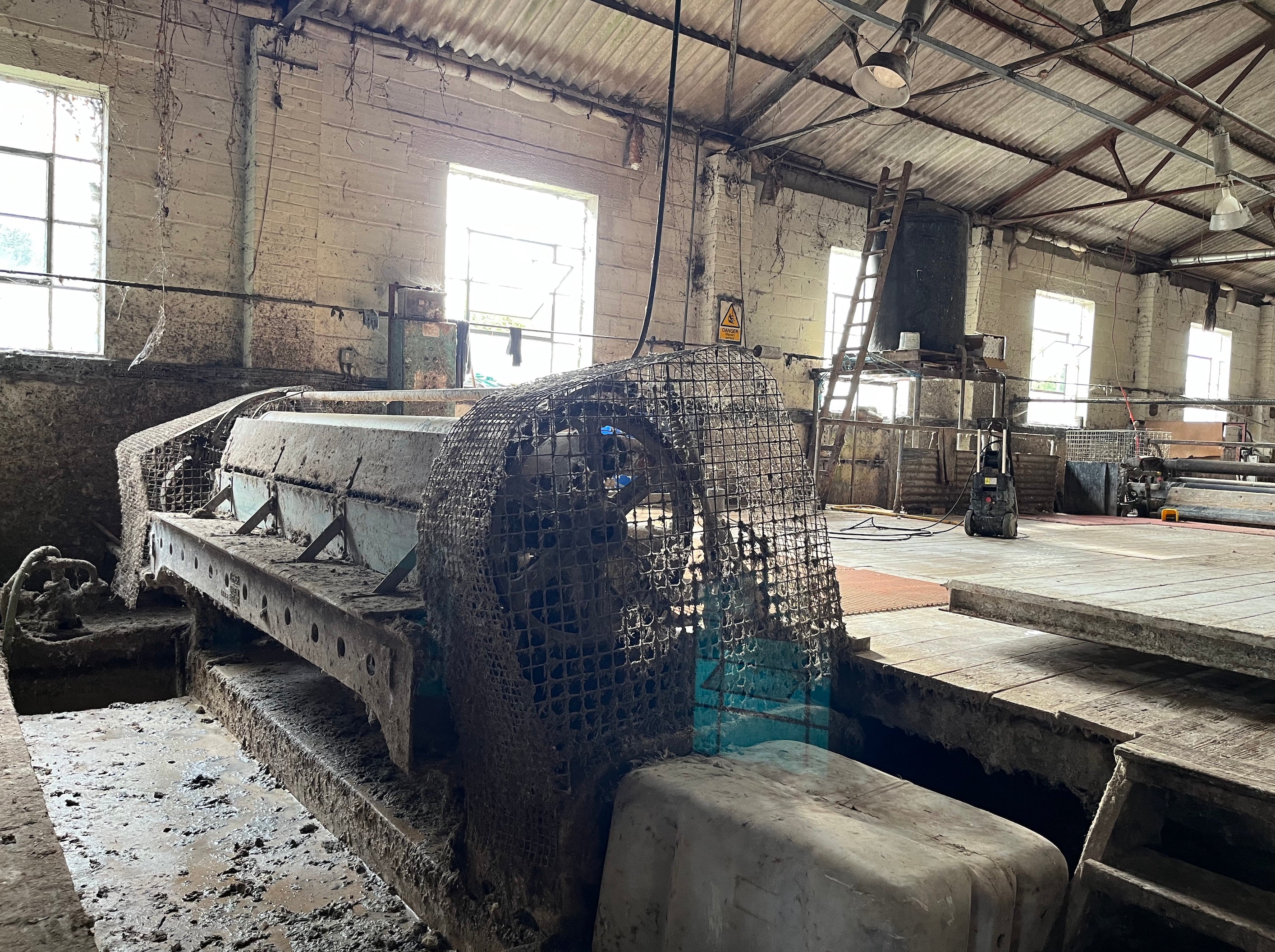
It is difficult to put into words the amount of time and love and passion that goes into creating each and every individual hide.
First of all, the salted raw hides must be rehydrated and then de-haired and have any fat removed from the flesh side. This process takes a couple of weeks. The hides are sourced from Devon cows and are a byproduct of the meat industry.
There is a stream that flows alongside the tannery, it is water from this stream along with oak bark from the lake district and Wales that makes the tan liquor.
The oak bark is a waste product of the timber industry. It dries for three years before being crushed in a machine powered by a water wheel.
The only other ingredient is time.
Each hide is suspended in the oak bark and water tan liquor for around 12 months. It is this very slow and natural process which not only leaves all the character of the hide intact, but also preserves the fibres and produces the strongest leather with the highest tensile strength.
Each individual hide is inspected and any last remaining bits of hair or fat are removed by hand.
The leather is then dried. Baker's even have an ingenious way to turn the waste fat and unusable leather trimmings into energy to assist the drying process.
The hides are now ready to be rolled and then finished. Andrew kindly demonstrated how each bridle butt must be rolled on this incredible old machine with a brass roller, manually adjusted to just the right settings. This is yet another labour intensive and highly skilled process.
There are a number of different finishing processes depending on the desired result and end destination for the leather.
The bridle leather we use is hand dyed and then finished with dubbin or tallow to help keep the leather supple. Whilst the Russia Kip is finished with a distinctive cross grain and dressed with birch oil. Some clients even have their own signature finishes.
Leave a comment
Comments will be approved before showing up.